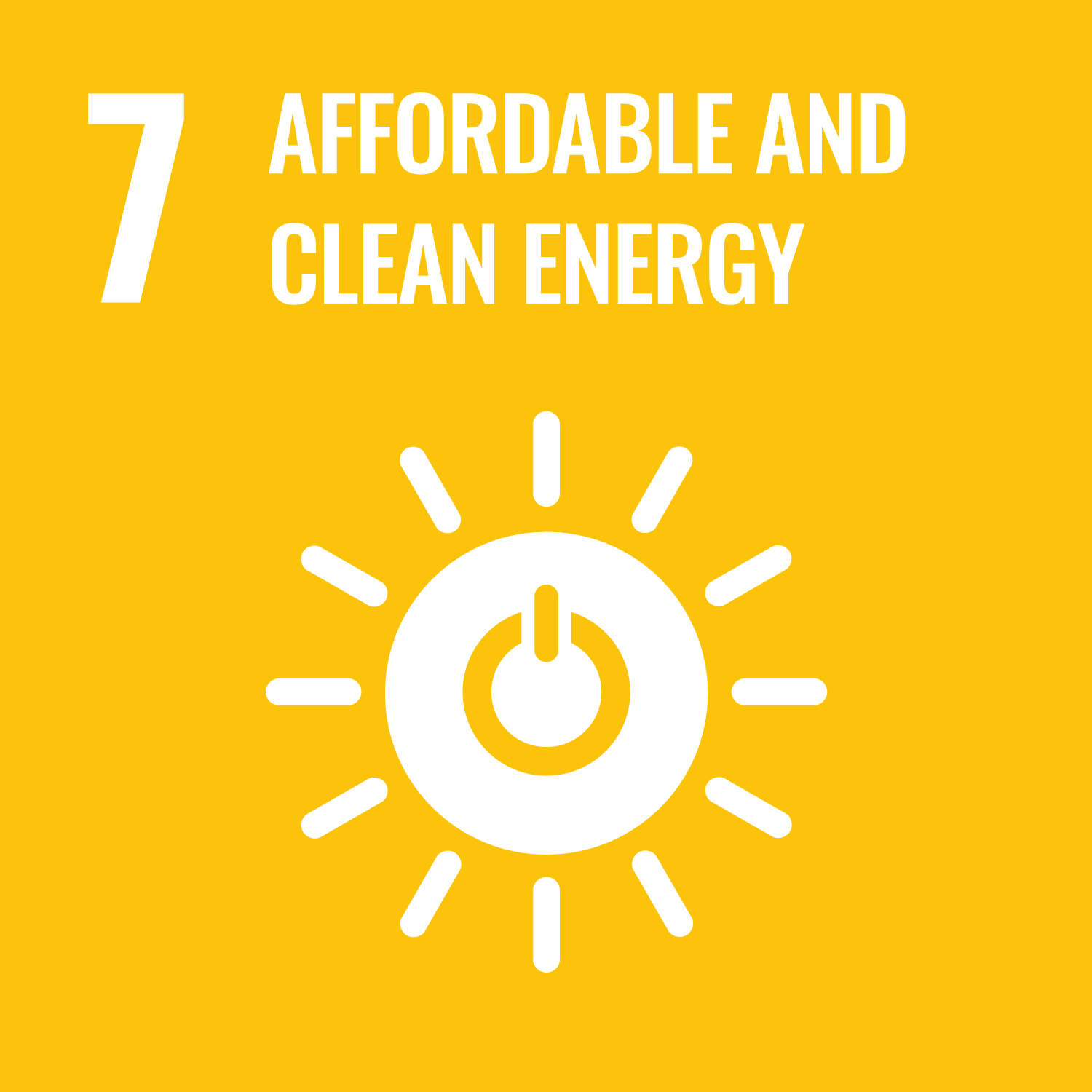
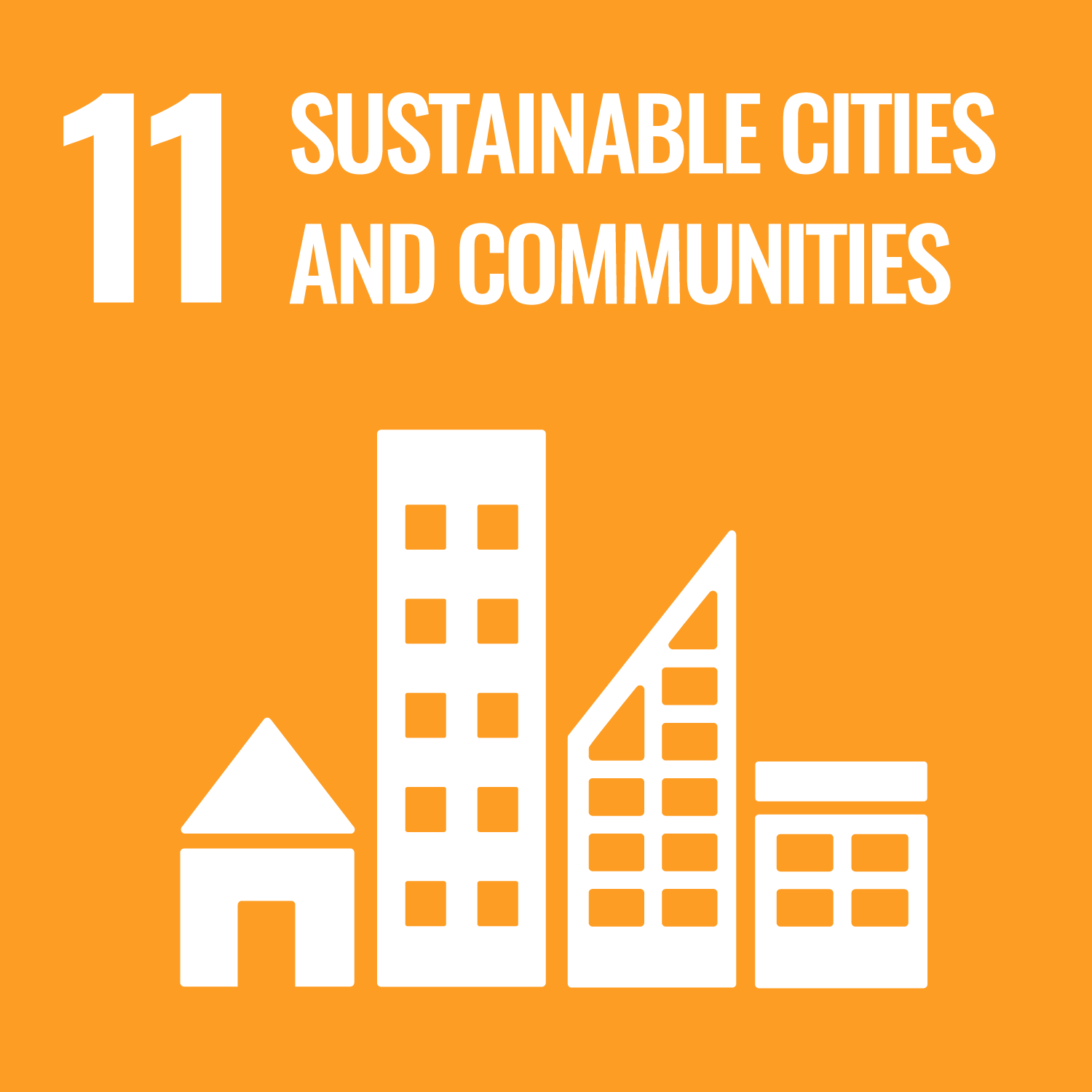
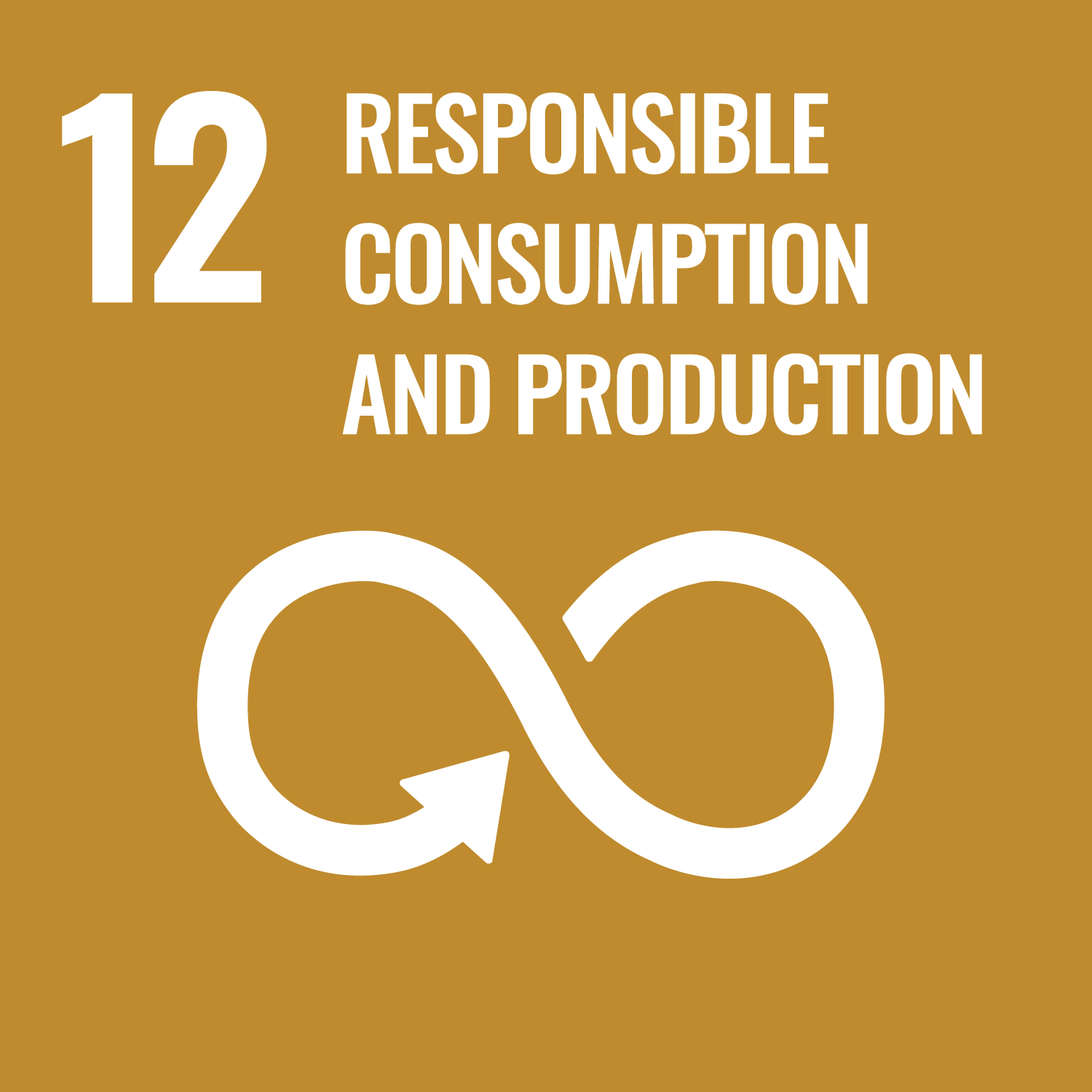
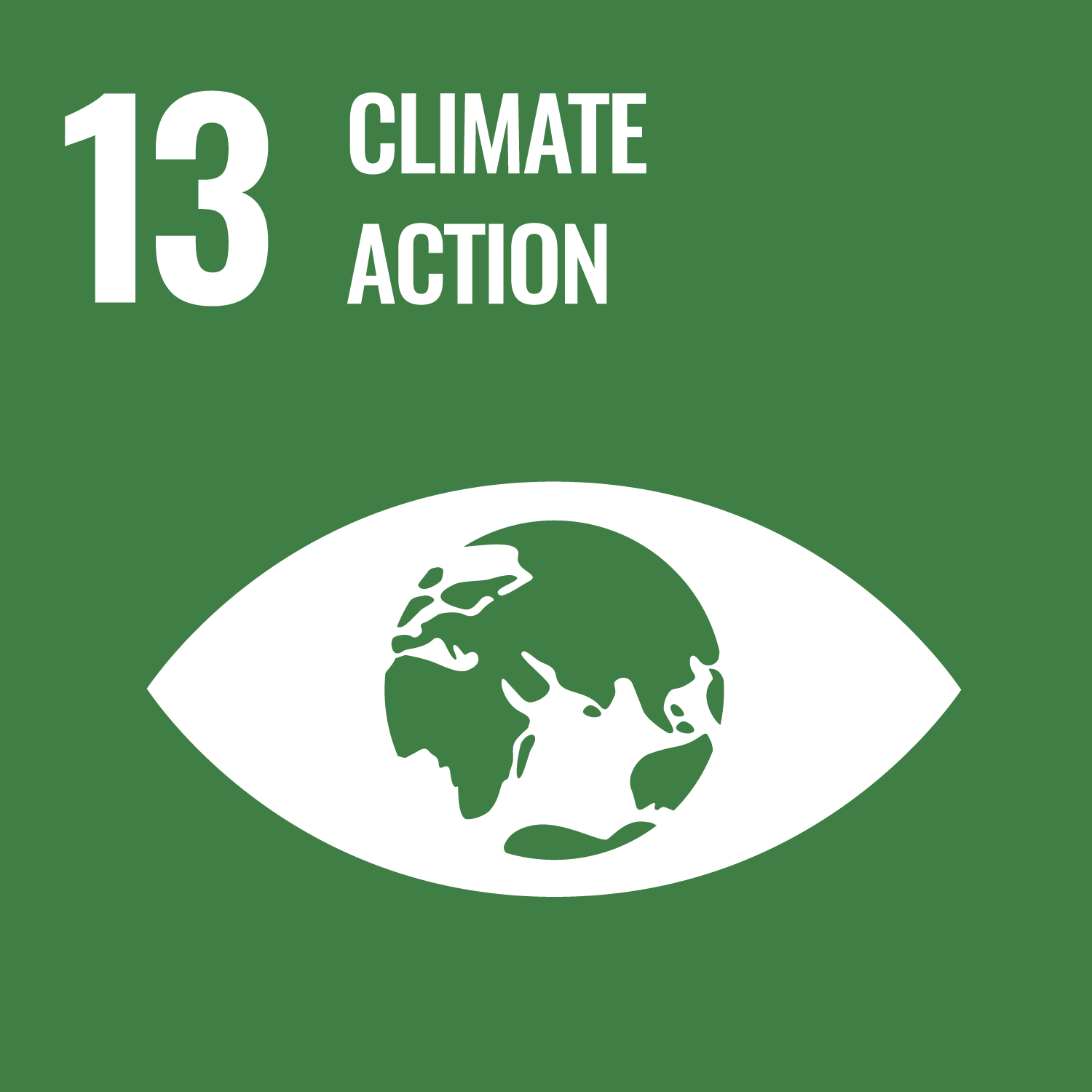
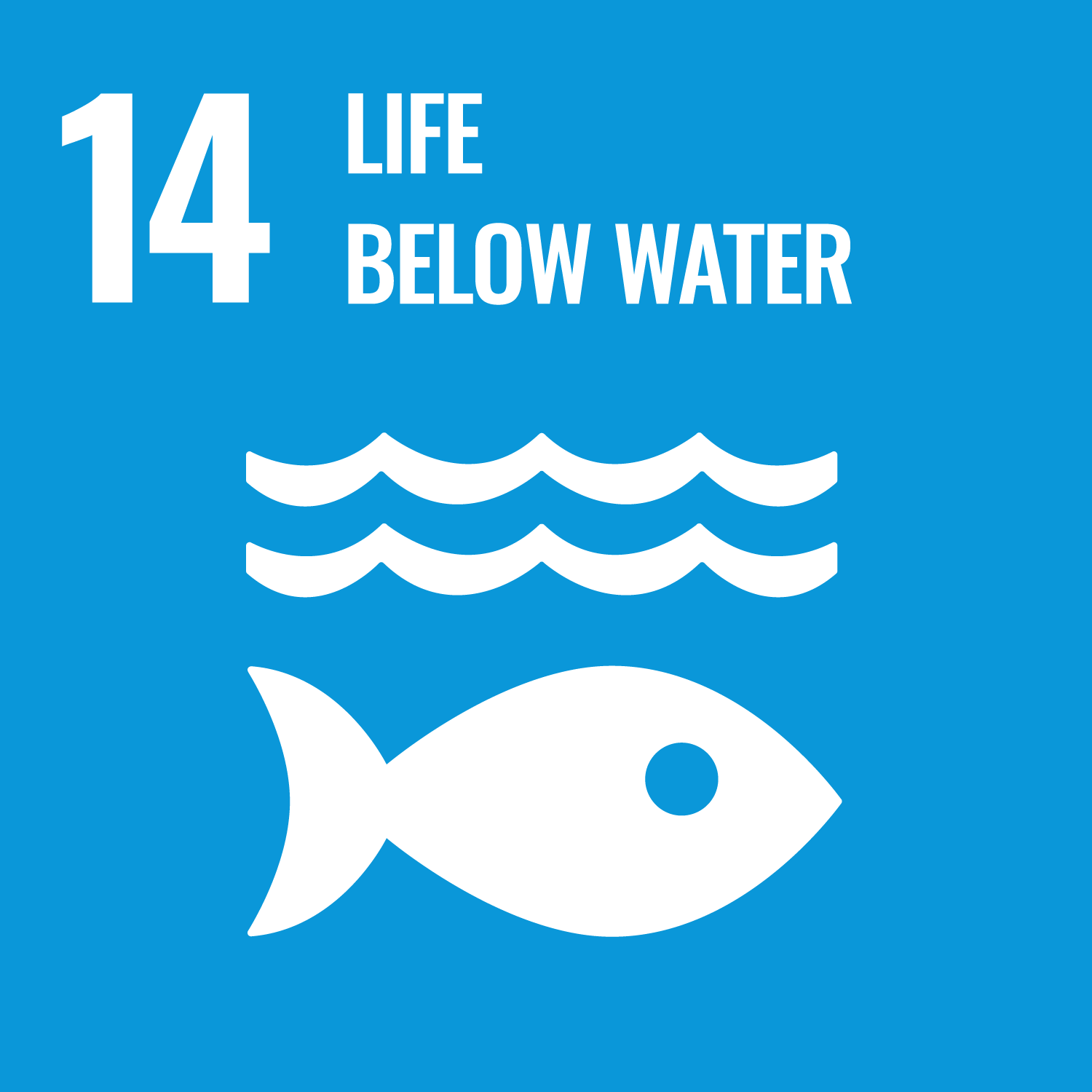
Recycling of waste plastics
Recently, the percentage of waste plastics in Japan that are recovered and recycled has exceeded 80%. However, this is attributed mainly to the increased amount of energy that is thermally recovered through the utilization of combustion heat . The percentages of plastics that undergo material or chemical recycling have remained flat. Thermal recovery is an effective means of reducing the amount of fossil resources that are used to generate power. However, to build a society with zero carbon emissions, we need to reduce the amount of CO2 emitted from the combustion of fuel and waste plastics which are made from fossil resources. The recycling of waste plastics is mainly divided into three categories.
- Material recycling: Cleaning, crushing, and pelletizing waste plastics, melting them, and making them into products again
- Chemical recycling: Decomposing plastics into their components at a phase in the middle of plastic synthesis to recycle them back into their chemical substances
- Thermal recovery: Combusting waste plastics to recover thermal energy

Chemical recycling enables us to significantly reduce our use of fossil resources.
Waste plastics may be difficult to recycle back into products if they contain different materials or impurities. This is not the case with chemical recycling, which uses chemical reactions to decompose waste plastics into constituent molecules to form chemicals.
If we promote chemical recycling and enable the reuse of waste plastics as chemical raw materials, we will significantly reduce the amount of fossil resources consumedused and create an ideal 3R cycle. This will also lead to the significant reduction of CO2 emissions from the processing of waste plastics.
Recycling waste plastics back into resources using EBARA's proprietary gasification technologies
EBARA Environmental Plant possesses two chemical recycling technologies.
One is EUP® a two-stage pressure gasification system developed jointly with Ube Industries, Ltd. This system uses the combination of cracker and two pressurized gasifiers to accelerate thermal decomposition reactions. This enables the collection of higher-quality gases than gasification under normal pressures, even from waste plastics containing different materials and impurities, providing raw materials which can be used to generate chemicals such as ammonia and ethylene. In addition, among the non-incombustibles contained in waste plastics, metals can be recovered and recycled in an unoxidized state while fly ash is melted away in the high-temperature gasifier, taken out as slag, and reused as roadbed material for roads, etc. Presently, this system is operating at the plastic recycling facility (KPR) of Showa Denko K. K. in Kawasaki City, Kanagawa, with a recycling capacity of 64,000 tons/year.
The other technology is ICFG®, an internally circulating fluidized-bed gasification system we developed on our own. It features a furnace divided into a gasification chamber and a combustion chamber. The bed material (sand) is internally circulated to enable the efficient thermal decomposition of input materials, from which combustible gases and oils are recovered. Combustible gases and oils obtained using this system can be used as chemical raw materials for the generation of naphtha and other materials. They can also be used as fuels for power generation. Similar to EUP®, this system is also capable of processing waste plastics containing different materials or impurities. It can also recycle biomass into chemical raw materials.
EBARA Environmental Plant will contribute to the realization of a sustainable society through the societal implementation of chemical recycling.
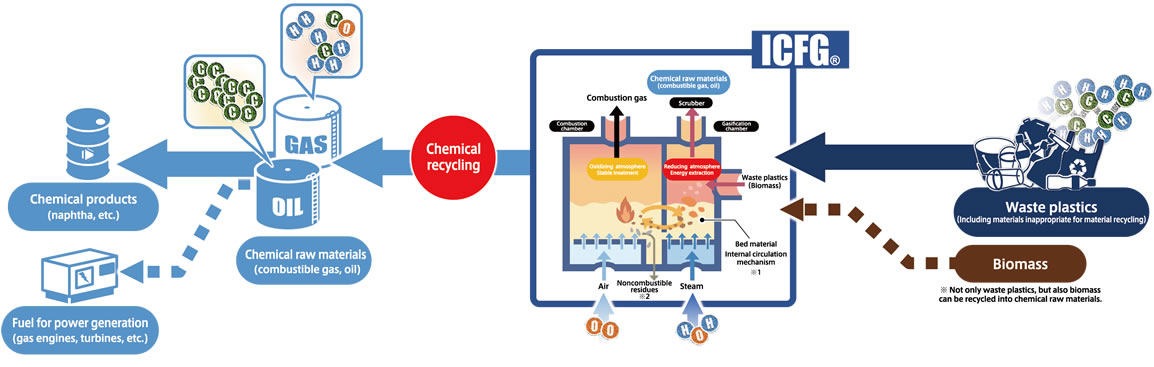
*ICFG is a registered trademark of EBARA Environmental Plant Co., Ltd. in Japan.