Operations & Maintenance
- Artificial Intelligence (AI)
- Remote Support
- Robots
Remote Support
Conventionally, experienced operators have reliably operated waste treatment facilities using their own skills and their five senses. In the future, it will be necessary to operate facilities reliably and in ways that emit less carbon dioxide and have a smaller environmental impact. To address the shortage of working population and the diversification of the employees, it will be necessary to develop advanced operations control technologies that are independent of human skill. To enhance the security, safety and stability of facility operations and thereby fulfill their responsibilities to society and serve the local community, it will be essential to fully leverage artificial intelligence (AI), the Internet of Things (IoT) and other cutting-edge technologies.
To increase stability and advance the technology used in the operation of waste incineration facilities, we opened the Fujisawa Remote Support Center in June 2016 and the Haneda Technical Support Center in June 2018, respectively. We then began providing real-time operations support services for waste incineration facilities.
The Fujisawa Remote Support Center has operators specializing in remote operations support so that operational support can be provided in real-time. The Haneda Technical Support Center has a team of dedicated engineers who can adjust control parameters and provide maintenance support. Capitalizing on their locational advantages, the two facilities play different roles in their provision of remote support.
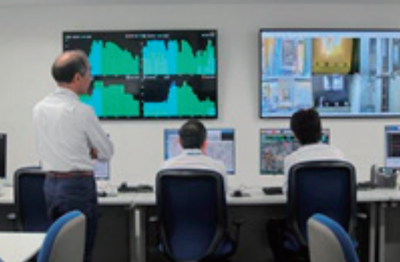
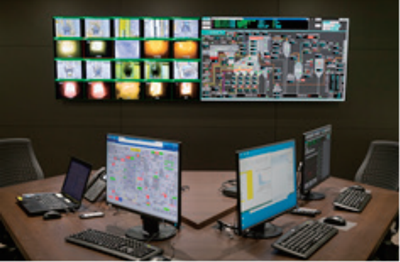
Main support from the Fujisawa Remote Support Center
1. Alarm monitoring
Operators at the Fujisawa Remote Support Center monitor whether or not proper response actions are taken when an important alarm is triggered, to prevent any abnormal measurements, alarms or other signals from being overlooked and avoid errors in operations.
2. Alarm management
They analyze the number of alarms triggered and the details of the alarms and events on a weekly basis to determine if it is necessary to respond and determine what corrective actions are needed to prevent less important alarms and increase the quality of operations management.
3. Assessment of operation status
They evaluate the volume of waste treated, the concentration of hazardous substances in exhaust gases, utility consumption and other indicators that are significant in operations management on a weekly basis and produce weekly reports for individual facilities. The weekly monitoring and management of operational status help facilities deal with failures at an early stage.
4. Assessment of operations status
They assess whether or not the operators of waste incineration facilities are carrying out furnace operations in accordance with established standards when they make manual intervention. We train these operators to make proper manual intervention and regularly revise furnace operations standards to incorporate the operators' knowledge.
Main support from Haneda Technical Support Center
1. Streamlining control adjustments
Formerly, dedicated engineers visited sites to set up and adjust different control parameters associated with automatic plant control. Now, set up and adjustment can be carried out from the Haneda Technical Center to streamline the control adjustment process.
2. Advancement in assessment of operation status
A system for supporting the assessment of the status of operations using a business intelligence (BI) tool has been developed to streamline and standardize the processes of quantitatively evaluating the status of operations and proposing improvements at the Fujisawa Remote Support Center.
3. Maintenance support using wearable cameras
Video and audio captured by wearable cameras worn by facility operators and maintenance staff are shared in real-time with dedicated engineers at the Haneda Technical Support Center. The engineers provide individual facilities with remote inspection support and emergency maintenance support to enable swift responses to equipment failures and prevent the unscheduled suspension of operations and other problems.